Metal 3D Printing | The Future of Manufacturing?
Welcome to an exciting journey through the world of metal 3D printing! Today, we're going to dive into the process of transforming fine steel powder into a highly intricate hydraulic manifold using the state-of-the-art TRUMPF TruPrint 3000.
Table of Contents
- 1. Introduction
- 2. Loading Steel Powder
- 3. 3D Printing the Hydraulic Manifold
- 4. Cleaning & Recapping Cylinders
- 5. Setting Up Supply & Build Cylinders
- 6. De-Powdering the Hydraulic Manifold
- 7. Revealing the 3D Printed Manifold
- 8. Designing the 3D Hydraulic Manifold
- 9. Why Choose 3D Printing?
- 10. Testing the Printed Part
1. Introduction
When you look at what resembles sand, don’t be deceived; it’s actually metal powder! It’s so fine that caution is key while handling it since it can easily get inhaled. Today, we’re using 316L stainless steel for our hydraulic manifold because its lower carbon content enhances corrosion resistance.
2. Loading Steel Powder
[Music]
Let’s get started by loading this fine metal powder into our supply cylinder!
3. 3D Printing the Hydraulic Manifold
Our print process just finished, and it’s now time to ensure all excess powder is swept back into the build cylinder. We’ll cap it off to safely transfer it to the de-powdering station.
4. Cleaning & Recapping Cylinders
One of the standout features of the TRUMPF TruPrint 3000 is the ability to add a second cap on top of the first. This is crucial to maintain the nitrogen within the print chamber. Once capped, we can move the build cylinder away for the de-powdering process!
5. Setting Up Supply & Build Cylinders
With our empty build cylinder ready, we’re linking it to our sieve station. This system will allow us to recycle the leftover powder efficiently, filtering it back into our supply cylinders for future prints.
6. De-Powdering the Hydraulic Manifold
Once at the de-powdering station, we’ll use a clamp to flip the build cylinder upside down. This method effectively removes the leftover powder while our printer continues working on the next project, ensuring optimal use of time.
7. Revealing the 3D Printed Manifold
[Music]
Now for the most exciting part—revealing the printed hydraulic manifolds! The design comes to life through innovative engineering from LEAP 71, using an algorithmic approach to ensure proper structure and support.
8. Designing the 3D Hydraulic Manifold
These manifolds are designed with specific criteria in mind, such as wall thickness, port size, and minimum overhanging angles. The algorithm prevents collisions and optimizes the placement of support struts.
9. Why Choose 3D Printing?
So why print hydraulic manifolds in 3D? Here are a few key benefits:
- Weight Reduction: 3D printing allows for lightweight designs without sacrificing strength.
- Compact Design: Our manifolds can fit into tighter spaces, enhancing overall system efficiency.
- Streamlined Channels: Curved channels minimize pressure drops compared to traditional designs.
- Material Efficiency: Additive manufacturing only uses material where it’s needed, reducing waste significantly.
10. Testing the Printed Part
Before we wrap up, let’s test the durability of our newly created part! You might be surprised at how resilient these prints are.
[Applause] [Laughter]
It’s noteworthy that you can even use the build plate to fixture parts for additional machining, leveraging its solid connection to the printed components!
Thank you for joining us on this stairway to the future of manufacturing! Remember, you can connect with our community on Discord, access our free educational content, and dive deeper into the fascinating world of CNC and 3D printing! Hit that like button and subscribe for more amazing content!
Connect With Us! | Links |
---|---|
Join our Community Discord | Join here |
CNCEXPERT Profile | Create a Free Profile |
Follow on Instagram | Follow Us |
More Articles
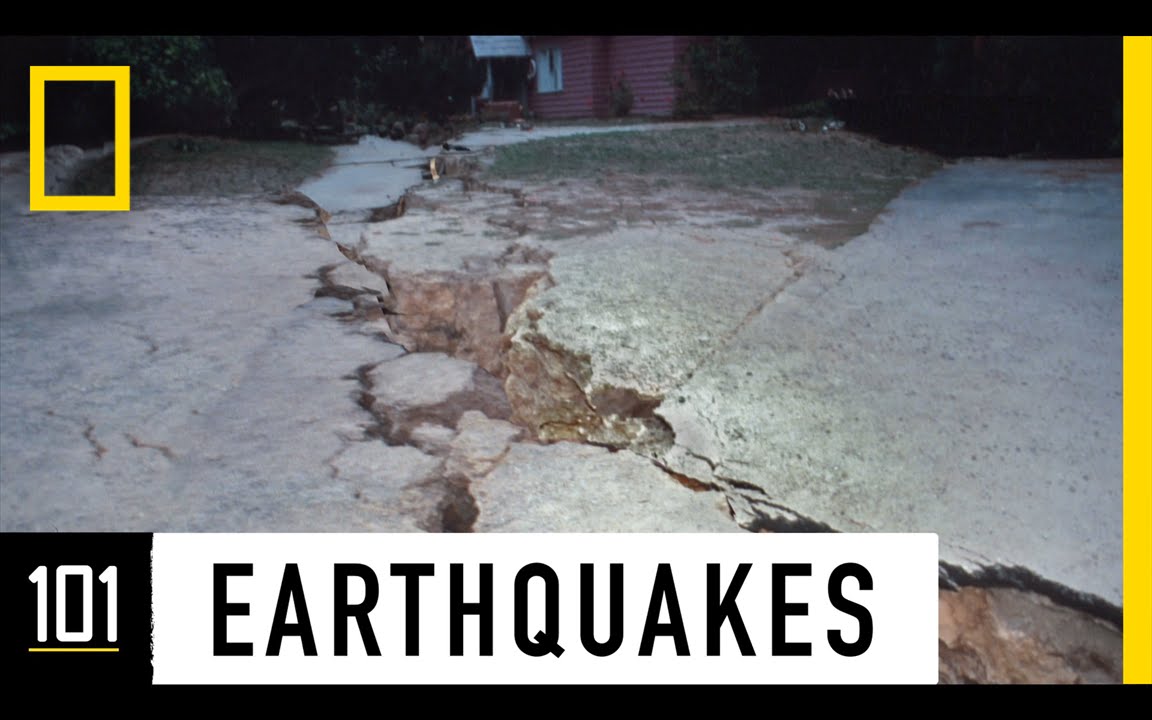
Earthquakes 101 | National Geographic
National Geographic
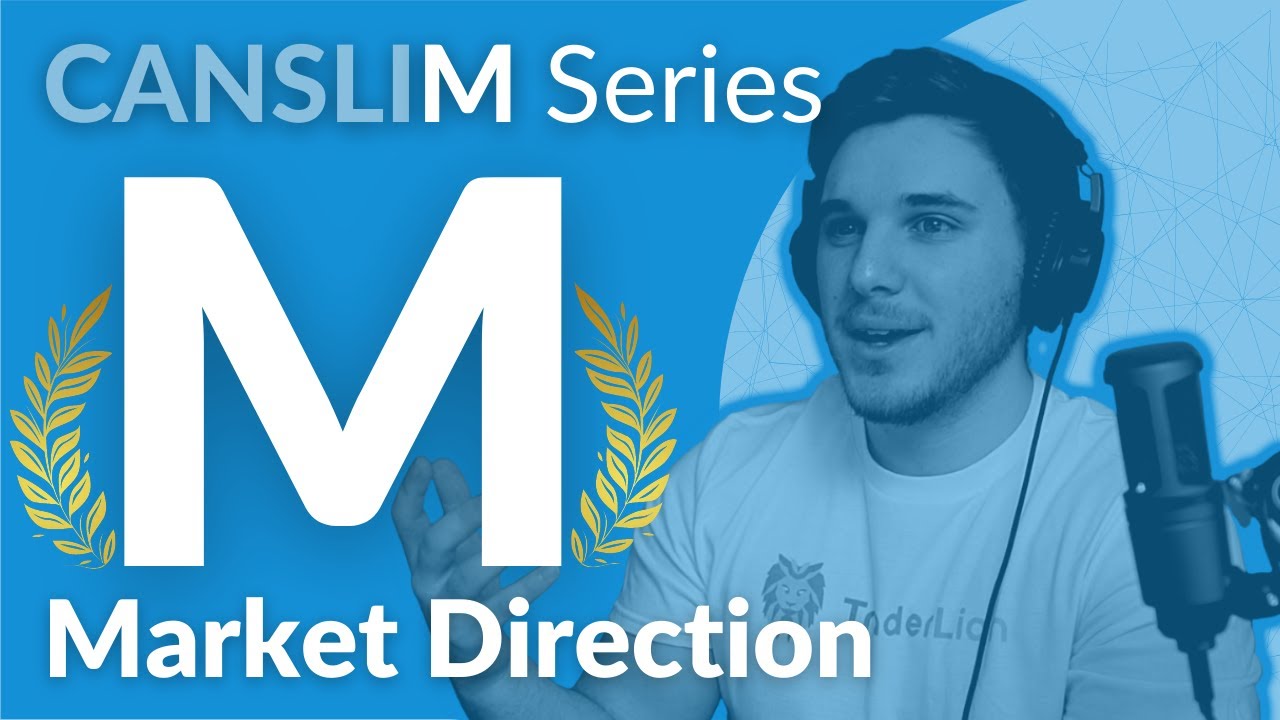
CANSLIM Investing Strategy: This "M" Factor is CRITICAL to Avoid Big Losses (M in CANSLIM)
TraderLion
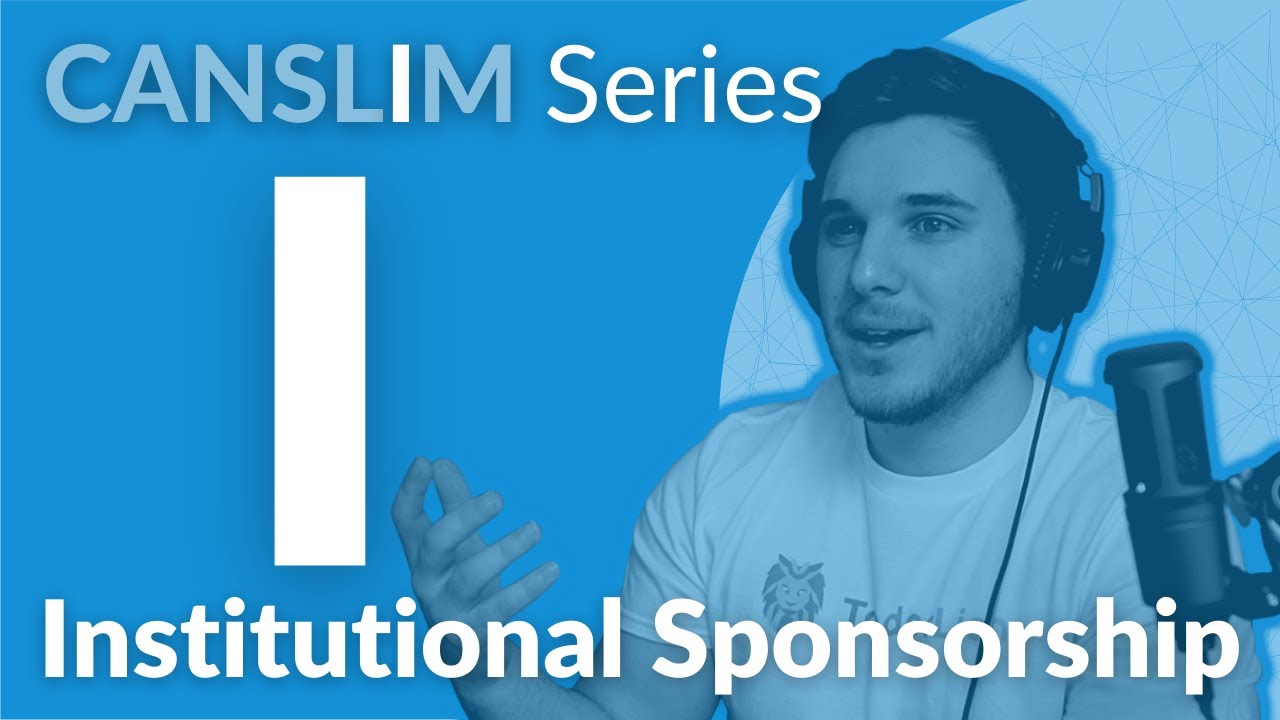
CANSLIM Investing Strategy: This "I" Factor Predicts HUGE Stock Gains (I in CANSLIM)
TraderLion
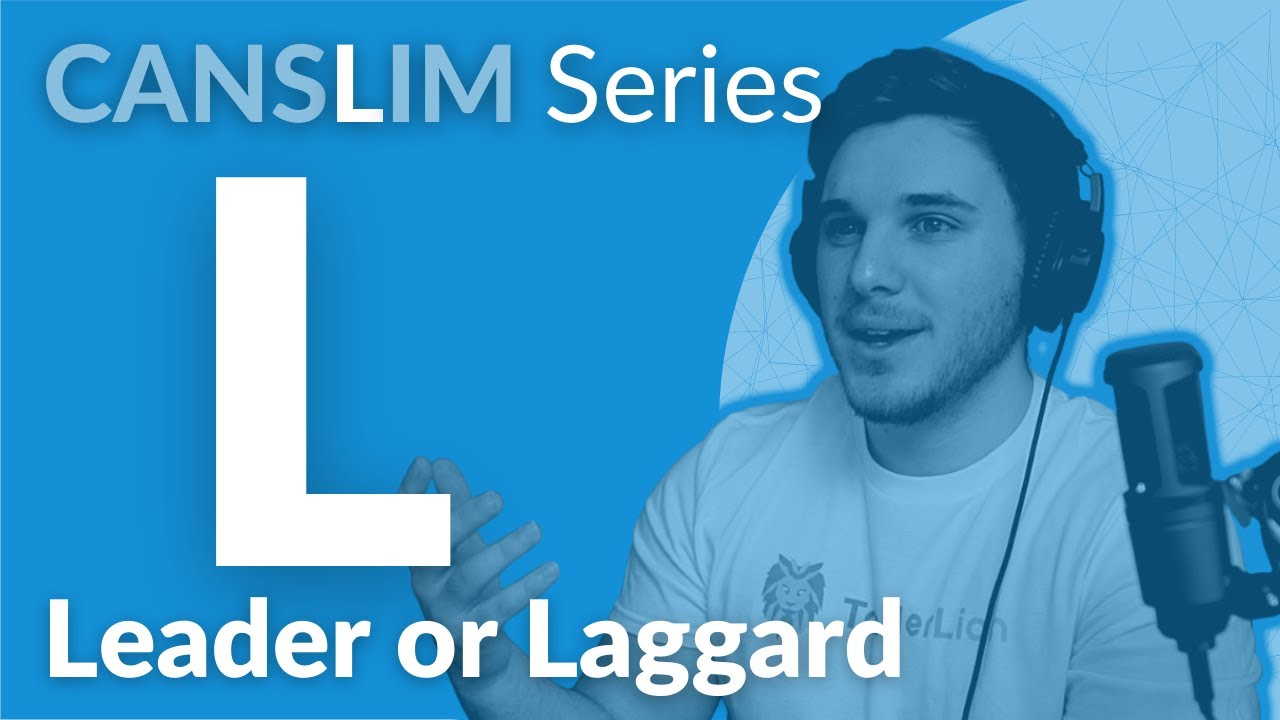
CANSLIM Investing Strategy: How to Spot Next BIG STOCKS using this Strategy (L in CANSLIM)
TraderLion
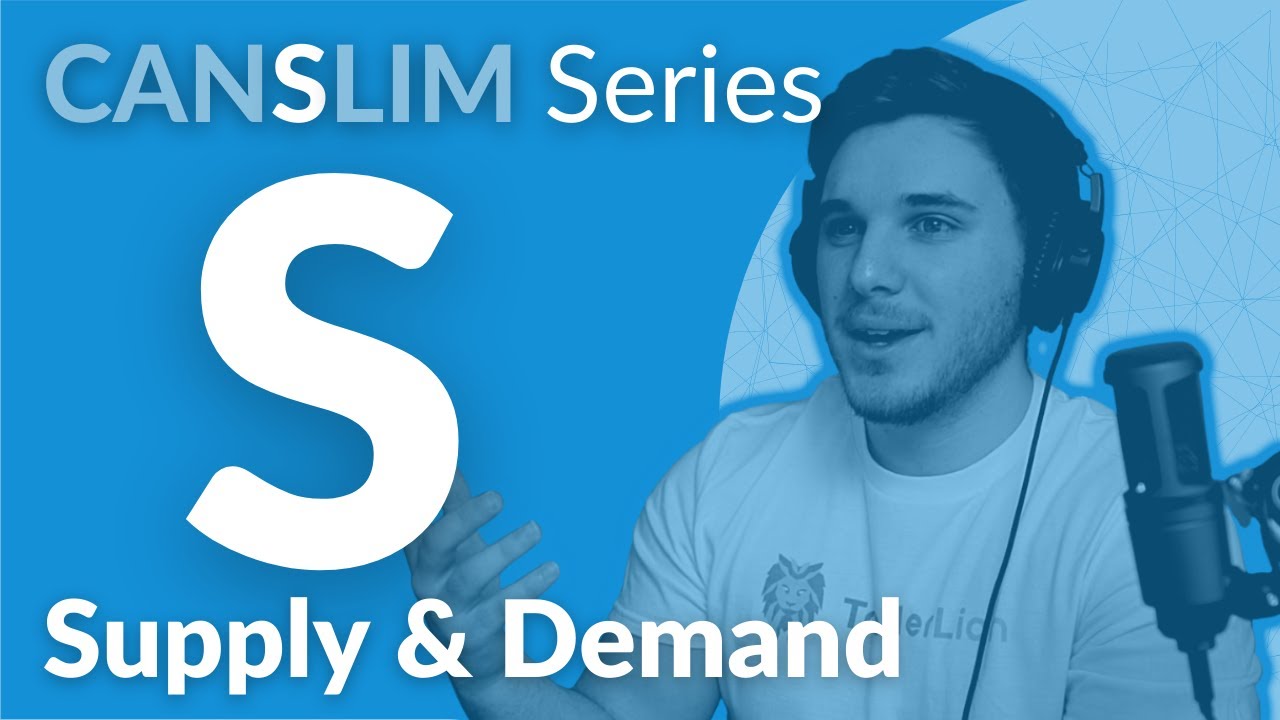
CANSLIM Investing Strategy: Use Supply & Demand to Find the Next 1000% Gainer (S in CANSLIM)
TraderLion
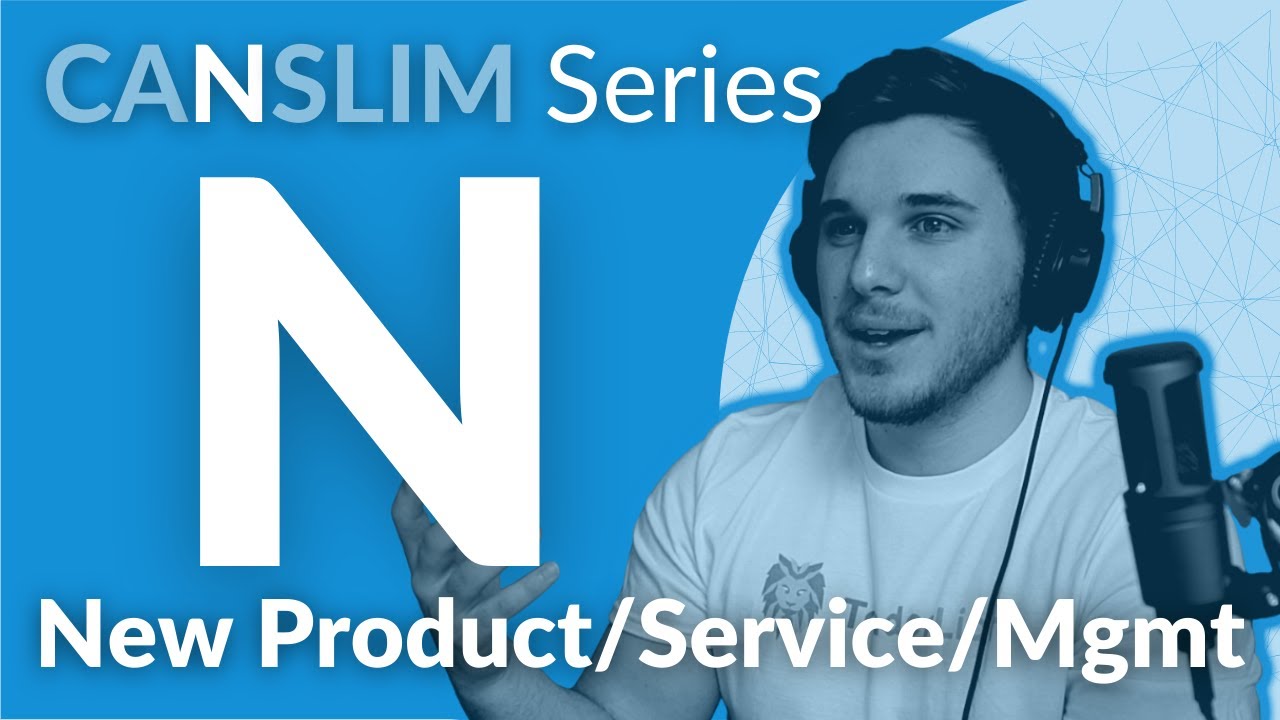
CANSLIM Investing Strategy: All 1000% Gain Stocks Have This in Common (N in CANSLIM)
TraderLion